Forklift Fork Inspection - Ansi Standard
6.2.8 Inspection and Repair of Forks in Service on Fork Lift Trucks
(a) Forks in use shall be inspected at intervals of not more than 12 months (for single shift operations) or whenever any defect or permanent deformation is detected. Severe applications will require more frequent inspection.
(b) Individual Load Rating of Forks. When forks are used in pairs (the normal arrangement), the rated capacity of each fork shall be at least half of the manufacturer's rated capacity of the truck, and at the rated load center distance shown on the lift truck nameplate.
6.2.8.1 Inspection.
Fork inspection shall be carried out carefully by trained personnel with the aim of detecting any damage, failure, deformation, etc., which might impair safe use. Any fork that shows such a defect shall be withdrawn from service, and shall not be returned to service unless it has been satisfactorily repaired in accordance with para. 6.2.8.2
(a) Surface Cracks. The fork shall be thoroughly examined visually for cracks and if considered necessary, subjected to a nondestructive crack detection process, special attention being paid to the heel and welds attaching the mounting components to the fork blank. This inspection for cracks must also include any special mounting mechanisms of the fork blank to the fork carrier including bolt-type mountings and forged upper mounting arrangements for hook or shaft-type carriages. The forks shall not be returned to service if surface cracks are detected.
(b) Straightness of Blade and Shank. The straightness of the upper face of the blade and the front face of the shank shall be checked. If the deviation from straightness exceeds 0.5% of the length of the blade and/or the height of the shank, respectively, the fork shall not be returned to service until it has been repaired in accordance with para. 6.2.8.2
(c) Fork Angle (Upper Face of Blade to Load Face of the Shank). Any fork that has a deviation of greater than 3 deg from the original specification shall not be returned to service. The rejected fork shall be reset and tested in accordance with para. 6.2.8.2.
(d) Difference in Height of Fork Tips. The difference in height of one set of forks when mounted on the fork carrier shall be checked. If the difference in tip heights exceeds 3% of the length of the blade, the set of forks shall not be returned to service until repaired in accordance with para. 6.2.8.2.
(e) Positioning Lock (When Originally Provided). It shall be confirmed that the positioning lock is in good repair and correct working order. If any fault is found, the fork shall be withdrawn from service until satisfactory repairs have been effected.
(f) Wear
(1) Fork Blade and Shank. The fork blade and shank shall be thoroughly checked for wear, special attention being paid to the vicinity of the heel. If the thickness is reduced to 90% of the original thickness, the fork shall not be returned to service.
(2) Fork Hooks (When Originally Provided). The support face of the top hook and the retaining faces of both hooks shall be checked for wear, crushing, and other local deformations. If these are apparent to such an extent that the clearance between the fork and the fork carrier becomes excessive, the fork shall not be returned to service until repaired in accordance with para. 6.2.8.2.
(g) Legibility of Marking (When Originally Provided). If the fork marking in accordance with para. 7.27.2 is not clearly legible, it shall be renewed. Marking shall be renewed per instructions from original supplier.
6.2.8.2 Repair and Testing
(a) Repair. Only the manufacturer of the fork or an expert of equal competence shall decide if a fork may be repaired for continued use, and the repairs shall only be carried out by such parties.
It is not recommended that surface cracks or wear be repaired by welding. When repairs necessitating resetting are required, the fork shall subsequently be subjected to an appropriate heat treatment, as necessary.
(b) Test Loading. A fork that has undergone repairs other than repair or replacement of the positioning lock and/or the marking, shall only be returned to service after being submitted to, and passing, the tests described in para. 7.27.3, except that the test load shall correspond to 2.5 times the rated capacity marked on the fork.
ng lock and/or the marking, shall only be returned to service after being submitted to, and passing, the tests described in para. 7.27.3, except that the test load shall correspond to 2.5 times the rated capacity marked on the fork.Tags: forks inspection osha
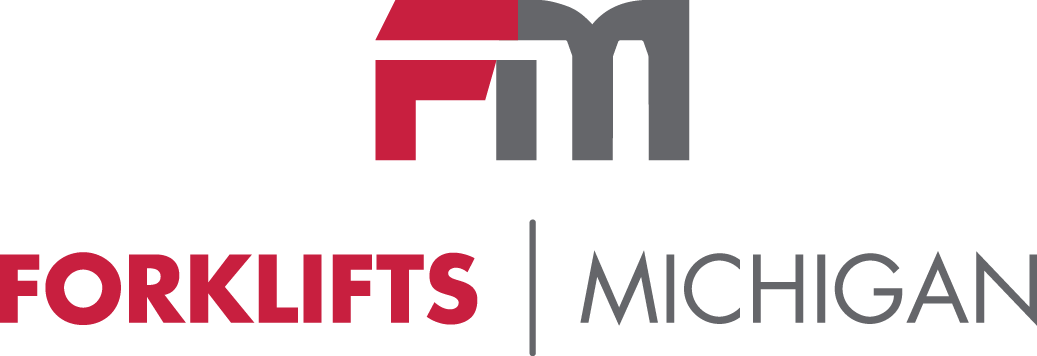